Realizacje | Wtrysk IML
NIEUSTANNIE BARDZIEJ DOSKONALI...
ZOBACZ NASZE WYBRANE REALIZACJE!
Uzyskaj natychmiastowe odpowiedzi na najczęściej zadawane pytania...
CEL
Celem opracowania nowego lub udoskonalonego wyrobu jest znalezienie rozwiązania dobrego technicznie i zapewniającego ekonomiczną produkcję.
WERYFIKACJA
Sprawdzianem dla dokonanych założeń i zrealizowanych działań jest uruchomienie procesu technologicznego i rozpoczęcie produkcji wyrobu.
DZIAŁANIE
Procesowi przetwórstwa TS (technologiom) nierozłącznie towarzyszą wszelkiego rodzaju peryferia (urządzenia pomocnicze) w postaci silosów, dozowników, podajników, urządzeń chłodzących, termoregulatorów, itp.
PROJEKT WALIZKA + TECHNOLOGIA IML
Projekt: WALIZKA + TECHNOLOGIA IML
Wtryskiwanie z wykorzystaniem technologii etykietowania w formie wtryskowej (IML – ang. In Mold Labeling) jest specjalną metodą łączącą w jednym cyklu formowanie i zdobienie wyrobu końcowego. Technologia ta jest stosowana jest w branży opakowaniowej (ale nie tylko) i uznawana za „dekoracyjną”. Wtryskiwanie metodą IML zaczyna się od wprowadzenia do wnętrza formy wtryskowej odpowiednio ukształtowanej etykiety, najczęściej z naniesionym wzorem graficznym. Może ona także zawierać elementy nie będące tworzywem, na przykład folię metalową.
Do zamkniętej formy, w której znajduje się pozycjonowana etykieta z folii, następuje wtryśnięcie tworzywa, a etykieta utrzymywana przy ściankach formy, zostaje trwale połączona z wypraską wtryskową w wyniku równoczesnego działania wysokiego ciśnienia i temperatury tworzywa oraz dzięki siłom adhezji. Po ochłodzeniu i wyjęciu z formy wypraska z etykietą tworzą jednorodny element.
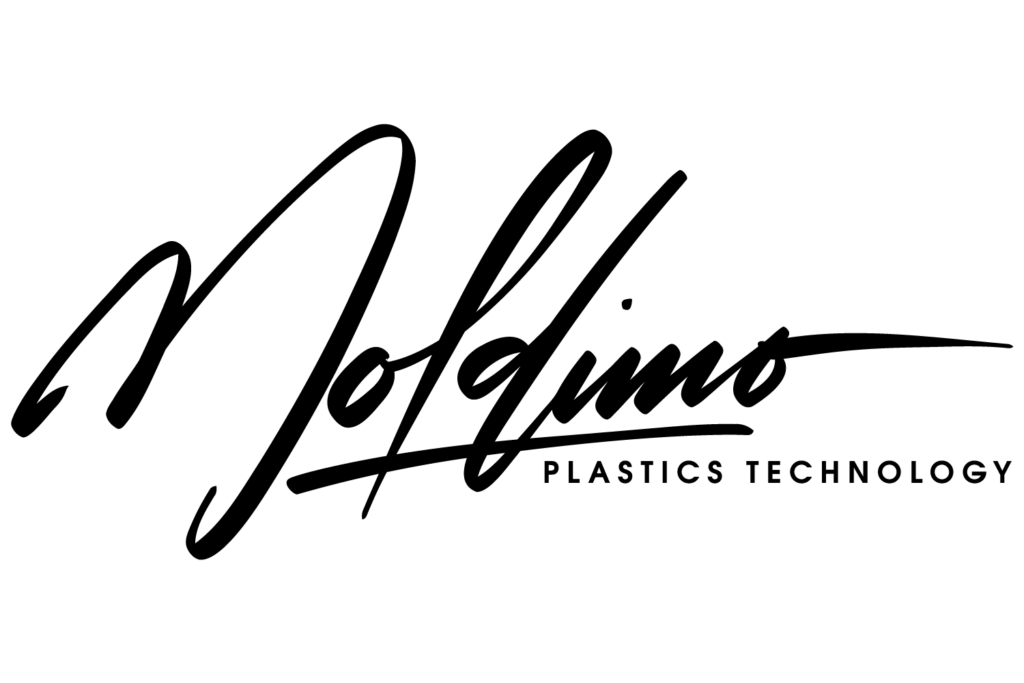
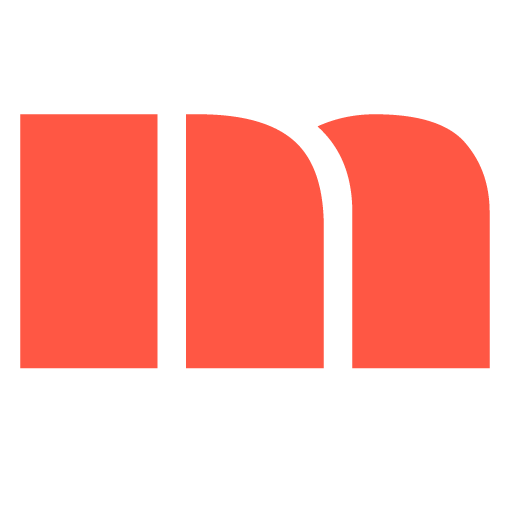
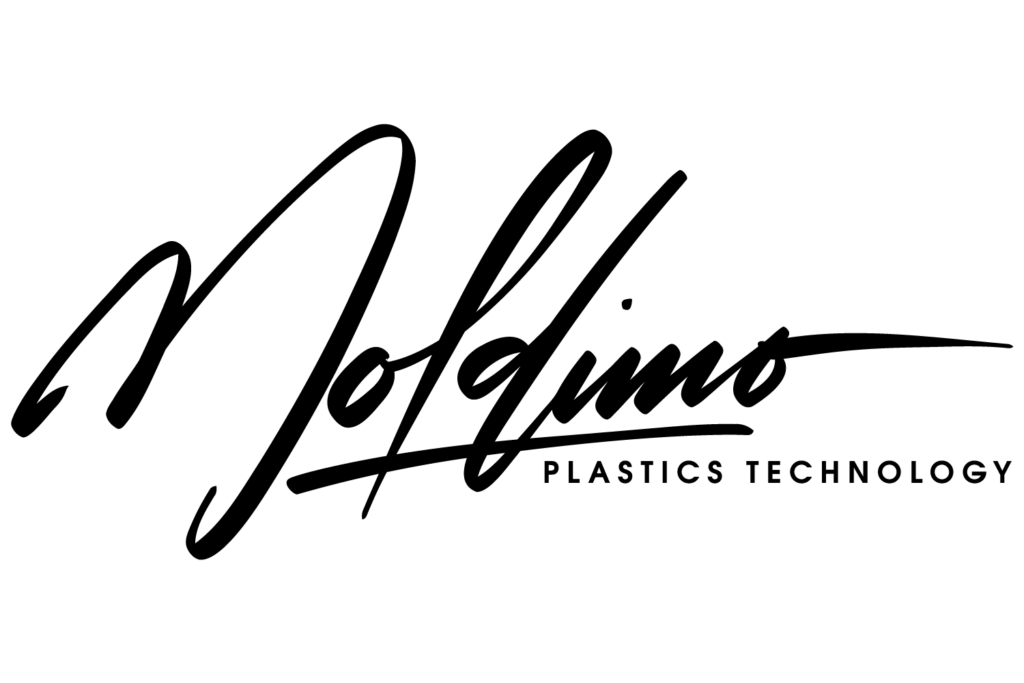
Projekt: WALIZKA + TECHNOLOGIA IML
Cel – zastosowanie technologii IML w celu podniesienie atrakcyjności detalu poprzez umieszczenie etykiety na zewnętrznej stronie wyrobu.
- Forma na wtryskarkę o sile zwarcia formy 200T
- Wtrysk z technologią IML dająca możliwość aplikacji etykiety foliowej w matrycy podczas cyklu wtryskarki.
- Zastosowanie technologii IML i jej zalet – znaczna przewaga trwałości połączenia etykiety do detalu vs standardowe naklejanie poza cyklem wtrysku oraz zwiększenie dokładności pozycjonowania etykiety względem detalu.
NAJCZĘŚCIEJ ZADAWANE PYTANIA (FAQ)
Poniżej lista najcześciej zadawanych pytań dotyczących przygotowania i uruchomienia procesu produkcyjnego wyrobów z TWORZYW SZCZTUCZNYCH.
Jeśli macie Państwo inne prosimy o kontakt telefoniczny lub mailowy (z wykorzystaniem poniższego formularza) - z chęcią na nie odpowiemy!
Przetwórstwo tworzyw sztucznych jest bardzo wyspecjalizowanym procesem i tak naprawdę zaczyna się już na etapie designu powiązanego m.in. z doborem materiału, a każdy następny proces jest ściśle związany z otrzymaniem końcowego produktu. Sam proces produkcyjny jest również bardzo wymagający i musi być realizowany przez wyspecjalizowanych technologów z użyciem odpowiedniego i kosztownego sprzętu oraz wyposażenia. Sam fakt, że w branży przetwórstwa mamy jeszcze wiele różnorodnych specjalizacji, technologii formowania oraz setki możliwych do zastosowania materiałów wskazuje, że temat nie jest prosty.
Najlepszym sposobem jest przygotowanie profesjonalnej analizy, która zdefiniuje dane brzegowe. Pośród nich należy wymienić m.in. podstawowe funkcje produktu i jego graniczne parametry takie jak: oczekiwana cena produktu, nabywcy, użytkownicy, potencjał, miejsca dystrybucji, czynniki kulturowe, sposób użytkowania, planowana długość życia na rynku, możliwości lub konieczność recyklingu.
Pośród parametrów decydujących o ocenie projektu należy wymienić takie jak: jakość wykonania, funkcjonalność, odpowiedni dobór materiału, trwałość, estetyka, efekt ekonomiczny.
Jednymi z najistotniejszych elementów mających na celu zwiększenie szans powodzenia danego pomysłu rynkowego, w tym nowych wyrobów z tworzyw sztucznych, są: ustalenie grupy docelowej, jej rozmiar i potrzeby, a także najważniejszych funkcjonalności i warunków, w jakich ma być wykorzystywana dana aplikacja. Zweryfikowanie pomysłu na wczesnym etapie i zrozumienie użytkowników to pierwszy krok do stworzenia wyrobu rynkowego dostarczającego rzeczywistą wartość.
NIE. Należy pamiętać, że każda technologia ma swoje uwarunkowania i idące z nimi w parze ograniczenia. Kluczowym elementem dla potrzeb określenia optymalnej technologii i sposobu wytwarzania danego detalu jest szczegółowa analiza wszelkiego rodzaju założeń i wymagań względem wyrobu przeprowadzona przez doświadczoną osobę z branży.
Posiadanie takiego zaplecza może mieć sens wówczas, kiedy planujemy realizację bardzo dużej liczby projektów, a na ich wdrożenie chcemy poświecić odpowiednie nakłady czasu, środków finansowych i zaplecza ludzkiego. Należy pamiętać, że koszty specjalistycznego sprzętu do przetwórstwa oraz koszty wytworzenia narzędzi do ich formowania należy określić ogólnie jako „wysokie”. Natomiast w przypadku pojedynczych projektów prostszym rozwiązaniem jest zwrócenie się do firmy, która zrealizuje cały projekt „od początku do końca”, biorąc na siebie odpowiedzialność za wytworzenie gotowego wyrobu, zgodnego z określonymi wymaganiami.
Pierwszą i orientacyjną kalkulację wyrobu można wykonać po zamknięciu projektu 3D (modelu) naszego wyrobu znając dodatkowe informacje związane z materiałem, technologią formowania, kosztem narzędzi i oprzyrządowania jak również zakładaną wielkością (skalą) produkcji. Sposób kalkulacji i wynikający z niego jednostkowy koszt wytworzenia będzie istotnie powiązany z tym parametrem.
Na każdym etapie projektu można wykonać próbę wyceny na podstawie znanych już założeń i informacji. Musimy jednak wziąć pod uwagę możliwość wystąpienia określonych rozbieżności. Jeśli dana faza projektu nie jest zakończona i istnieją czynniki które mogą wpłynąć na nią cały projekt będzie nadal ewoluował włącznie z wyceną wyrobu.
Jako decydujące należy uznać takie kryteria jak: kształt, jakość i dokładność odwzorowania powierzchni (w tym tolerancje wymiarowe), przeznaczenie i warunki pracy, ilości produkcyjne, rodzaj materiału, wymagania szczegółowe, itp.
Forma wtryskowa to strategiczny czynnik w projekcie. Jej działanie polega na wtryskiwaniu ciekłego tworzywa do gniazda formy, które następnie zastyga i powstaje tzw. kształtka lub wypraska. Zjawiskom zachodzącym w formie oraz jej działaniu podporządkowane są wszystkie funkcje i parametry wtryskarki. W formie nie tylko kształtuje się geometria wyrobu, ale również powstaje właściwa tylko dla tej geometrii budowa wewnętrzna wyrobu.
Częstokroć koszt formy, zależny od stawianych jej wymagań, może być większy niż koszt samej wtryskarki a budowa wtryskarki czasem musi być dostosowana do budowy formy lub rodzaju produkcji. Niezależnie od stopnia skomplikowania każdą formę charakteryzuje budowa jej układów funkcjonalnych: technologicznych (bezpośrednio odpowiedzialnych za kształtowanie wyrobu) i mechanicznych (warunkujących prace formy jako narzędzia).
Model, który został zatwierdzony powinien z góry zakładać technologię jego produkcji oraz to, aby jego parametry nie zmieniły się podczas projektowania formy wtryskowej.
Jedną z najczęstszych przyczyn powstawania błędów przy produkcji wyrobów z TS jest nieznajomość właściwości przetwórczych tworzyw oraz zjawisk zachodzących w gnieździe formy. Określając geometrię wyrobu konstruuje się już gniazdo formy dostosowane do wtryskiwania określonej wcześniej odmiany tworzywa z określonymi płaszczyznami podziału, zbieżnościami i miejscami doprowadzenia tworzywa.
Bez wątpienia za kluczowe aspekty przy wyborze narzędziowni dotyczą poziomu technicznego oferowanych rozwiązań, posiadanego doświadczenia, specjalizacji (branżowa, technologiczna, itp.), terminów realizacji, relacji jakości vs. cena. Za najlepsze rozwiązanie należy uznać przypadek, w którym firma produkcyjna posiada własną narzędziownię.
Walidacja powinna zostać zakończona przed podjęciem decyzji o uruchomieniu produkcji formy wtryskowej.
W odróżnieniu od metali, własności użytkowe tworzywa jako materiału konstrukcyjnego kształtują się dopiero w czasie trwania procesu produkcyjnego, a właściwości wyrobu zależą od jego budowy wewnętrznej. W procesie wtryskiwania materiału termoplastycznego do formy wtryskowej budowa wypraski zależy od geometrii gniazda formy i zjawisk tam zachodzących podczas przepływu w fazie wypełniania a później chłodzenia sprężonej masy tworzywa.
Proces wtryskiwania składa się z kolejnych faz określających jego przebieg: 1) mających charakter mechanicznych (zamykanie formy, dojazd i odjazd cylindra wtryskowego, otwieranie i zamykanie formy, wypychanie wypraski) oraz 2) fazy technologiczne określające zmiany stanu tworzywa w cylindrze wtryskarki i przebieg zjawisk zachodzących w formie. Decydują one o geometrii i własnościach wypraski przebiegając w ściśle określonej kolejności, tj. faza wtrysku, faza, sprężania, faza docisku, faza chłodzenia, faza uplastyczniania.
Wtryskarka pełni rolę urządzenia produkcyjnego które powinno zostać prawidłowo dobrane do danej produkcji. Istnieje wiele typów wtryskarek różniących się nie tylko rozwiązaniami konstrukcyjnymi i rodzajem napędu (hydrauliczny, elektryczny, hybrydowy), ale również systemem sterowania. Dla wtryskarek o małej i średniej wielkości bardzo często są stosowane napędy elektryczne lub mieszane a ich podstawowymi zaletami są duża precyzyjność i dokładność pracy oraz mniejsze zużycie energii. Bezpośredni napęd elektryczny eliminuje obecność pośredniego nośnika energii jakim jest olej hydrauliczny.
Siła zwarcia maszyny jest nam niezbędna do utrzymania płyt formy podczas wtryskiwania pod dużym ciśnieniem. Innymi słowy maksymalna dostępna siła utrzymująca formę w stanie zamkniętym jest siłą zamykania wtryskarki z zależy ona od rzutu powierzchni wyprasek [cm²] oraz ciśnienia tworzywa w formie podczas wtrysku [bar].
Właściwy dobór wyposażenia wewnętrznego i zewnętrznego decyduje o możliwej do uzyskania jakości wyrobów i produktywności całego procesu w takim samym stopniu jak wybór wtryskarki wspomagając jej pracę. Do wyposażenia zewnętrznego zalicza się wszystkie urządzenia obsługujące i wspomagające pracę wtryskarki (dostawione lub dobudowane), w tym m.in.: roboty, separatory, transportery, urządzenia pakujące, młynki, suszarki, termostaty, dozowniki.
Zapraszamy do współpracy!